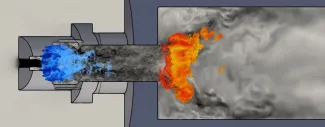
Scientific and industrial partners involved:
Cerfacs is a science center that produces innovative solutions for the simulation of earth physics and engineering. Backed by seven public and private partners, supported by European and national research projects, it is focused on research and training for high performance simulation. Cerfacs developed the simulation workflow.
Safran Aircraft Engines draws on a legacy reaching back over 110 years to design, develop, produce and market, alone or in partnership, engines for civil and military aircraft. It tested and deployed the workflow on one of their actual after-burner studies.
Codes involved:
AVBP: https://services.excellerat.eu/en/services/application-software/avbp/
PyHIP: https://pypi.org/project/pyhip/
Kalpataru: https://gitlab.com/cerfacs
Lemmings: https://pypi.org/project/lemmings/
Tekigo: https://pypi.org/project/tekigo/
Time period of the success story:
Prototype delivered in EXCELLERAT P2, ongoing deployment started in 2024
The decarbonation and depollution efforts of Safran Group are pushing the innovation of new burner technologies forward. However, the volume of after-burner flames and the unpredictability of newer fuels such as hydrogen are challenging the meshing practices. Indeed Hydrogen flames can be far thinner than Methane or Kerosene ones. The required high-resolution zones, extremely computer-intensive, must be kept as small as possible. A manual positioning is too difficult in complex configurations. On the other hand, direct remeshing on hydrogen flames is limited to research purposes, because it disregards the affordability of the generated grid. Finally the procedure of running a simulation, decide when to refine, set up the next simulation and start again cannot be done manually in an industrial context. This required automation and portability across machines, in other words: an integrated workflow.
The first step was the integration of the “Lemmings” tool developed during EXCELLERAT P1 for packaging run workflows, providing portability, low impact on queues, exhaustive logging, and traceability of job sequences, thus overcoming limitations of mere job schedulers. The second step was the creation of a resolution-independent remeshing criterium using Tekigo (a result from COEC). Finally, the robustness of PyHIP and the performance of Kalpataru, both remeshing tools backed by EXCELLERAT P2, pushed the solution to maturity.
The resulting Automated Static Mesh Refinement workflow (ASMR) developed by Cerfacs has been deployed and successfully tested by Safran engineers. It allows for fast exploration and feedback on new meshes directly based on the physical phenomena observed and computational resources available. The current sequential mesh adaptation (using pyHip) permits to process up to 200 million tetrahedrons. Cerfacs is currently working on parallel mesh adaptation.
Safran Group developed the capability to routinely execute high fidelity simulations during the after-burner design process. Without this workflow, the computational cost would have limited these simulations to exceptional runs on a case-by-case basis.
The same workflow is being evaluated for other Safran design fields: ignition phases, cruise runs, turbomachinery. An interesting feature is emerging: The meshes created by the workflow are born of physical meshing criteria, while meshing practices commonly used by industry outside this workflow come from years of experience. Comparing the two kinds of meshes is shedding a new light on present simulation practices.
The increased automation in the workflow also reduced user support requests through higher homogeneity and better traceability of simulation runs. Thus, this workflow, initially required by industrial users, is now also slowly gaining traction with academic users for simulations with lower technology readiness levels, especially for highly unpredictable hydrogen burners.
Benefits:
Affordable simulations: The simulation can be adapted to available resources because the number of final degrees of freedom is directly input by the user
Lower manpower: The automation decreases the need for run supervision, while the traceability and logs accelerate runtime. This saves up to three quarters (75%) of the supervision time previously necessary.
- Resource optimisation: The automation ensures a progressive and reasonable usage of resources. This avoids run outliers in performance or set-ups.
Success story Highlights:
Keywords: automated workflow, reactive simulation, high-fidelity meshing, after-burners, simulation automation
Technology: HPC Simulation Workflow
Sectors: Aeronautics, Energy, Manufacturing & engineering, Mechanical engineering
Contact:
Antoine Dauptain – Cerfacs – dauptain@cerfacs.fr
Luis Carbajal Carrasco – Safran Aircraft – luis.carbajal-carrasco@safrangroup.com