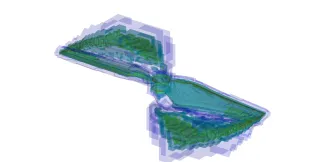
Scientific partners involved:
KTH is a leading Scandinavian research centre and the largest technical university in Sweden. It conducts research and education in engineering and technology, collaborating with prominent partners worldwide and participating in a variety of key projects.
Codes involved:
Neko https://neko.cfd/
Nek5000 https://nek5000.mcs.anl.gov/
Time period of the success story:
Adaptive Mesh Refinement (AMR) runs of the use case performed with AMR version of Nek5000 are ongoing and the first results should be ready in the middle of 2025.
The CPU version of AMR Neko is expected to be ready at the end of 2025 and a GPU version will be developed in 2026.
Scientific Challenge:
High-fidelity modelling of realistic, turbulent flows everyone encounter every day, like flows around various types of rotors, is challenging due to the wide range of the flow features that must be resolved. This makes running simulations computationally expensive and poses a meshing problem, as the flow dynamics may not be a priori known. A common solution is to use turbulence modelling, where small vortices are no longer resolved in the simulation, but their effect is approximated by a mathematical model. This lowers resolution requirements and thus reduces computational costs, but introduces modelling errors, making simulations of flows with complex dynamics less reliable. It is important to be able to perform high accuracy simulations of these complex flows since they could be used to develop new turbulence models.
Solution:
Cost of the numerical modelling is directly related to the mesh resolution and can be reduced by placing higher resolution only where it is needed. This can be effectively achieved by controlling computational error during runtime and by dynamically adjusting the mesh resolution accordingly. Such a workflow, called Adaptive Mesh Refinement (AMR), allows not only to reduce computational cost, but as well to model the flows with not a priori known dynamics. KTH is implementing an AMR workflow in the CFD solver Neko based on the Spectral Element Method (SEM). SEM can be considered a special version of widely known Finite Element Method. To implement AMR, they use native to SEM decomposition of the domain into non-overlapping spectral subdomains called elements, and perform recursive splitting/merging of these elements to create new ones. The resulting mesh is complex and requires special treatment of nontrivial combination of element’s interfaces, but allows one to complete the simulation at minimal cost increasing at the same time the robustness and reliability of the solution. An important aspect here is its efficient use of the computing resources.
Scientific impact:
AMR is a desirable feature of a CFD solver, enabling control of the computational error at optimal computational cost. It enables modelling flow cases with unknown dynamics, as the specific flow features can be captured through dynamic adjustment of the mesh during runtime. At the same time, meshing at the pre-processing step gets simplified and more generic grids can be created.
In addition, various tools and algorithms may need a simple method to increase local grid resolution, making AMR a useful solver component. An example could be an immersed boundary method (IBM), in which object surfaces are not represented directly by the mesh but rather modelled inside the computational domain. IBM provides a great deal of flexibility in modelling flows in complex geometric configurations without tedious meshing, but this requires sufficient resolution to mimic an object’s surface.
The significant reduction in computational cost and increased solution reliability will let researchers run bigger and more complex cases of industrial relevance. A good example is high-fidelity simulation of a drone rotor, which would give more insight into its flow dynamics and noise generation.
Benefits:
- Control of computational error at optimal computational cost
- Reduced mesh size resulting in reduced computational cost
- Simplified meshing and possibility to model flow cases with unknown dynamics
Success story Highlights:
Keywords: HPC, CFD, high fidelity simulations, spectral element method, adaptive mesh refinement, Neko
Technology: HPC
Sectors: Automotive, Aerospace
Contact:
Adam Peplinski, KTH, Royal Institute of Technology, adampep@kth.se